Now I have to apologize for being irritated!
Allow me to back up my apology by doing some good ...
I downloaded one of your designs. And I am looking at the first sketch, which is almost fully defined.
It contains one spurious line that is not constrained to anything. I am sure that was my accident, but I am going to take the opportunity to warn of overlapping lines. Avoid these as good as possible.
Imagine you'd have to sketch everything in ink on soft paper. You never want to go over the same line twice.
That is also a good practice when sketching in CAD.
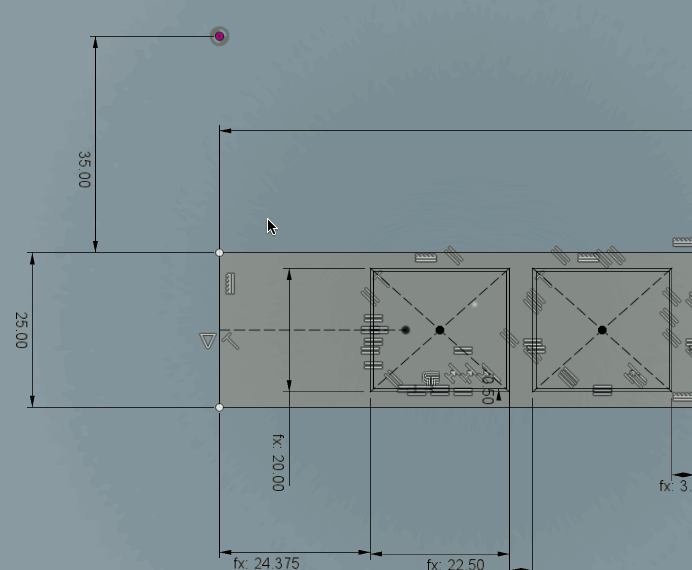
The second think I am noting is that you sketched the profile offset by a fixed distance of 35mm. Form a "standard" reusable part I would keep the origin of the design located at the center or corner of a face, vertex or body. This will often help not to have to create auxiliary construction planes for mirroring, or axis for patterning.
Also, if parts are symmetric it is usually a good idea to have the symmetries align with origin axis or planes.
You mention 6 parameters in another post. I believe you need another 2 parameters for the 3D rating clearance.
I am assuming these will likely be printing flat on the printer bed with a FDM printer. The tolerance in the Z axis is usually smaller than in the XY plane, hence 2 parameters.
In your sketch that would mean that you cannot use a uniform offset to allow for that clearance.
Another question you asked was in relation to sketches not being located in the component they should actually be in.
This can be done, but in your case you are too far along in the design and relationship exist between some entities in the component and outside of the component that prevent this from working. Unfortunately there are currently no tools available to untangle this.
It might not be a problem. You could simply continue in this design and use it only to great a small library of the tile variants you want to create. Then you can use a feature that was only recently introduced to Fusion 360. The Derive command allows to derive components from one design into another.
So you can derive one or more tile variants out of that small library into a new design and use it to build something with these tiles. the advantage this hs is that if you need to change the printer clearance, you change the user parameter for that in the library file and the designs with all the derived tiles will update to match.