I absolute love Adaptive Toolpaths and Vortex in Powermill, I try to run them as much as possible, I push my machine to the limit every day and strive for lower cycle times and better production.
One of the things I love everything about fusion is adaptive clearing, however there is one important thing thats been overlooked here. I see this often, and I wish I had a setting in my adaptive options to avoid this, when it leaves this tall, long and unridgid wall when clearing out material.
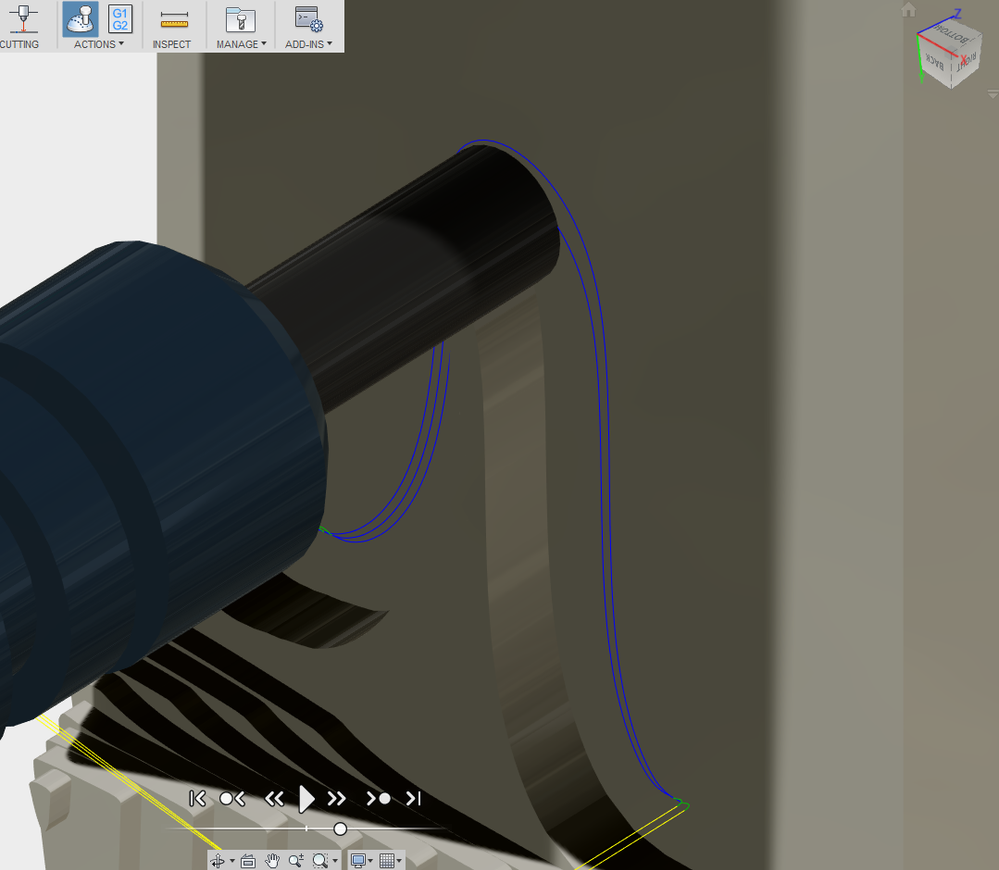
Id love to see in Fusion and HSM works an option to avoid this, where the toolpath would (when clearing all the material anyways) leave a set thickness to this wall (Say 1inch, so its rigid enough) then start from the end, working its way in, using slot clearing or a similar strategy, thus avoiding breaking ends, shooting thin sections all over the machine, or worse, pulling the wall into the tool and snapping a 1 inch carbide endmill running at 12 grand, 800 inch/ min.
I just took a photo, this is a very weak example of what is happening, but same idea. I often get it much worse, this is just a photo I took before writing this to illustrate the problem.
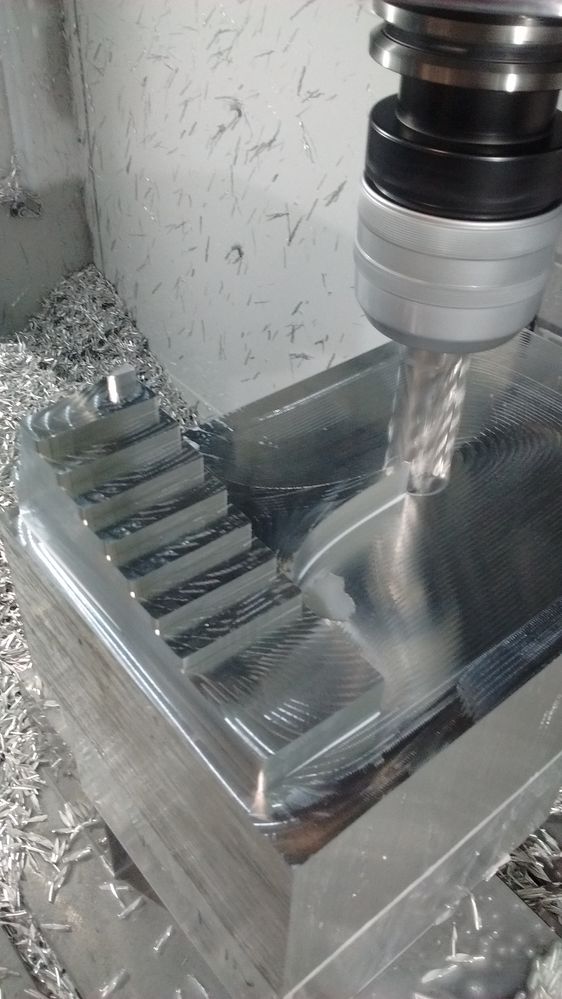
Thanks in advance for any input.